真空箱式爐淬火爐是一種利用真空技術(shù)進行熱處理的設(shè)備。其核心部分是一個密閉的爐膛,通常由耐高溫材料制成。爐膛內(nèi)部設(shè)有加熱元件和溫度控制系統(tǒng),用于對工件進行加熱和保溫。同時,爐膛外部還設(shè)有真空泵和管道系統(tǒng),用于抽取爐膛內(nèi)的空氣和其他氣體,形成真空環(huán)境。
在真空環(huán)境下,工件表面的氧化皮和油污等雜質(zhì)會被迅速揮發(fā)或分解,從而減少了工件表面的污染和氧化。同時,由于真空環(huán)境下的熱傳導(dǎo)效率較高,工件內(nèi)部的熱量能夠更均勻地傳遞到表面,從而實現(xiàn)快速加熱和冷卻。這種熱處理方式能夠顯著提高金屬材料的力學(xué)性能和耐腐蝕性。
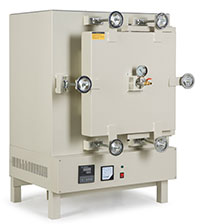
1.高精度控制:采用先進的數(shù)控系統(tǒng)和精密機械結(jié)構(gòu),能夠?qū)崿F(xiàn)對溫度、時間和壓力等參數(shù)的精確控制,確保熱處理效果的穩(wěn)定性和一致性。
2.高效節(jié)能:由于真空環(huán)境下的熱傳導(dǎo)效率高,能夠在短時間內(nèi)完成熱處理過程,降低了能耗和生產(chǎn)成本。
3.環(huán)保安全:在運行過程中不會產(chǎn)生有害氣體和粉塵,符合環(huán)保要求。同時,由于爐膛內(nèi)部為負壓狀態(tài),避免了爆炸和火災(zāi)等安全事故的發(fā)生。
4.適應(yīng)性強:適用于各種金屬材料的熱處理,特別是對于高合金鋼、不銹鋼等難加工材料的熱處理具有優(yōu)勢。
工藝流程:
1.準備工作:根據(jù)工件的材質(zhì)、形狀和尺寸等要求,選擇合適的熱處理工藝參數(shù),如溫度、時間和壓力等。
2.裝爐:將工件放入爐膛內(nèi),并關(guān)閉爐門。確保工件在爐膛內(nèi)的位置正確,避免相互碰撞和損壞。
3.抽真空:啟動真空泵,抽取爐膛內(nèi)的空氣和其他氣體,形成真空環(huán)境。通常需要達到一定的真空度才能開始加熱。
4.加熱:按照設(shè)定的溫度曲線,對工件進行加熱。加熱過程中需要實時監(jiān)測溫度變化,確保溫度控制在合理范圍內(nèi)。
5.保溫:當(dāng)工件達到預(yù)定溫度后,保持一段時間,使工件內(nèi)部的組織充分轉(zhuǎn)變。
6.冷卻:停止加熱后,采用適當(dāng)?shù)睦鋮s方式對工件進行冷卻。冷卻速度和方式的選擇取決于工件的材質(zhì)和性能要求。
7.出爐:當(dāng)工件冷卻至室溫后,打開爐門取出工件。對工件進行外觀和性能檢測,確保熱處理效果符合要求。
真空箱式爐淬火爐的優(yōu)勢:
1.提高產(chǎn)品質(zhì)量:能夠?qū)崿F(xiàn)高精度的熱處理效果,提高金屬材料的力學(xué)性能和耐腐蝕性。
2.縮短生產(chǎn)周期:由于真空環(huán)境下的熱傳導(dǎo)效率高,能夠在短時間內(nèi)完成熱處理過程,縮短了生產(chǎn)周期。
3.降低能耗:在運行過程中能耗較低,有助于降低生產(chǎn)成本。
4.環(huán)保安全:在運行過程中不會產(chǎn)生有害氣體和粉塵,符合環(huán)保要求。同時,由于爐膛內(nèi)部為負壓狀態(tài),避免了爆炸和火災(zāi)等安全事故的發(fā)生。